Paper making Sewage Treatment Processes
Paper is a ubiquitous material in our daily lives, providing immense convenience. However, the treatment of wastewater generated from the paper industry has emerged as a crucial issue, not only for the industry, but also for society at large. Failure to effectively address this problem is limiting the survival and growth of paper manufacturing enterprises. Utilizing waste paper for paper production not only conserves water and energy, but also minimizes chemical usage and reduces pollution compared to conventional paper made from plant fibers. Despite being less polluting than conventional paper production, the pulping and papermaking processes still produce significant amounts of pollutants such as BOD, COD, SS, toxicity, and chroma. These pollutants, combined with large water usage and high pollutant discharge loads, have resulted in severe environmental pollution problems. Therefore, wastewater treatment in waste papermaking has gained significant attention in response to stricter emission standards and water reuse requirements.
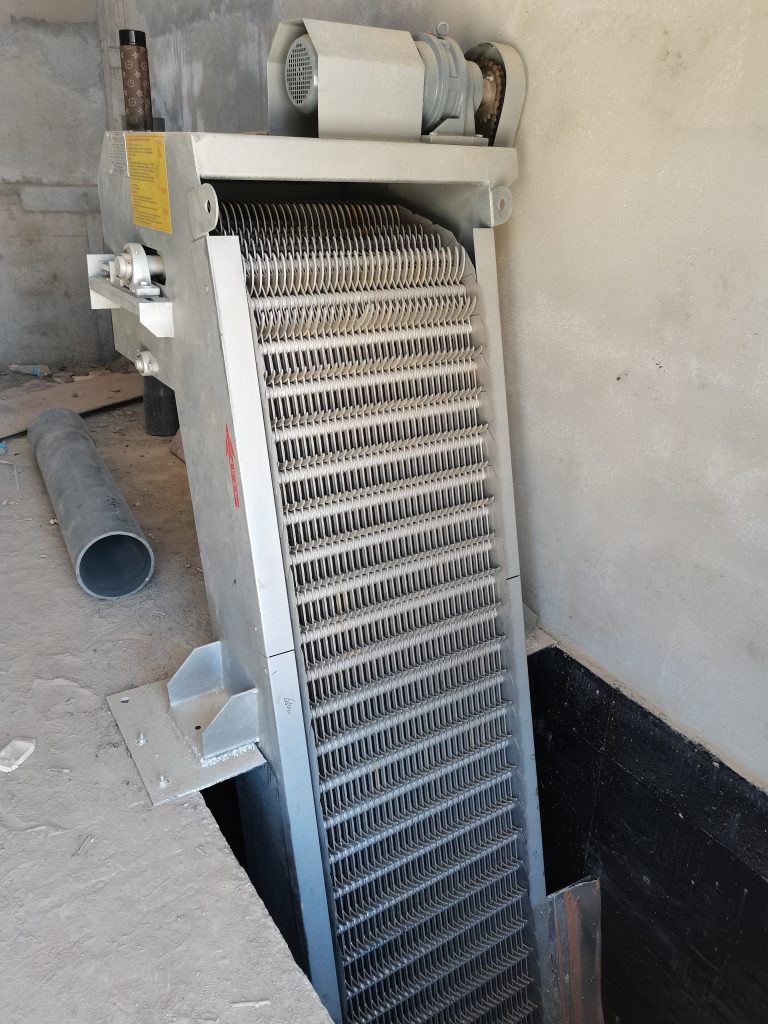
Wastewater quality analysis
一、Source of Paper-making Wastewater
The quality of wastewater is dependent on the volume of discharge and the amount of pollutants produced, which, in turn, are influenced by the raw materials and pulp yield. Additionally, the quantity of pollutants generated is linked to the additives utilized during the production process. For instance, not all organic chemicals used as additives or auxiliaries in the papermaking process are retained in the paper, and any portion that escapes into the wastewater can adversely impact water quality, leading to an increase in COD and other indicators. The primary source of adsorbable organic halides is chlorine-containing bleaching agents, disinfectants, and certain additives, such as wet strength agents. Thus, this standard specifies that the pollution resulting from pulp and paper wastewater should be evaluated based on several factors, including the type of raw materials, the number of chemicals added, the production process, the product type, the extent of treatment of reused wastewater, and the quantity of reuse. This determination can be made through material balance calculations.
二、Determination of wastewater quality for each production process:
1.Preparation wastewater
The contamination load of prepared wastewater varies greatly depending on the type of raw material and preparation method. For wood feed, COD, BOD and SS in wastewater are 0-10 kg/t pulp, 0-5 kg/t pulp and 0-8 kg/t pulp, respectively. For non-wood raw materials, COD, BOD and SS in wastewater are 20-60 kg/t pulp, 8-20 kg/t pulp and 30-80 kg/t pulp respectively.
2. Chemical pulp wastewater
Chemical pulp wastewater mainly includes cooking liquor, washing and bleaching wastewater, and overflow water generated during various stages of pulp production. Cooking liquor is the largest source of pollutants in the entire chemical pulp production process. For example, the black liquor produced in the alkaline pulping process concentrates almost 90 percent more than the contaminants produced in the pulp and paper process. It contains large quantities of degradation products of lignin and hemicellulose, pigments, pentose, residue alkali, and other leachates. The contamination load of the cooking liquor is closely related to the pulp yield and the conditions of the pulping process. The BOD, COD and SS for wastewater are 350-425 kg/t pulp, 1060-1,570 kg/t pulp and 235-280 kg/t pulp, respectively, due to the lower pulp yield of chemical pulp. After alkaline recovery, the contaminants in the wastewater produced by cold condensation are BOD and COD of 5-10 kg/t pulp and 10-30 kg/t pulp, respectively, and SS content is extremely low and negligible.
Washing and bleaching wastewater: The washing wastewater comes mainly from the residual cooking liquor of the unbleached pulp produced in the washing process. The pollutants discharged into the wastewater during this phase are called washout losses.
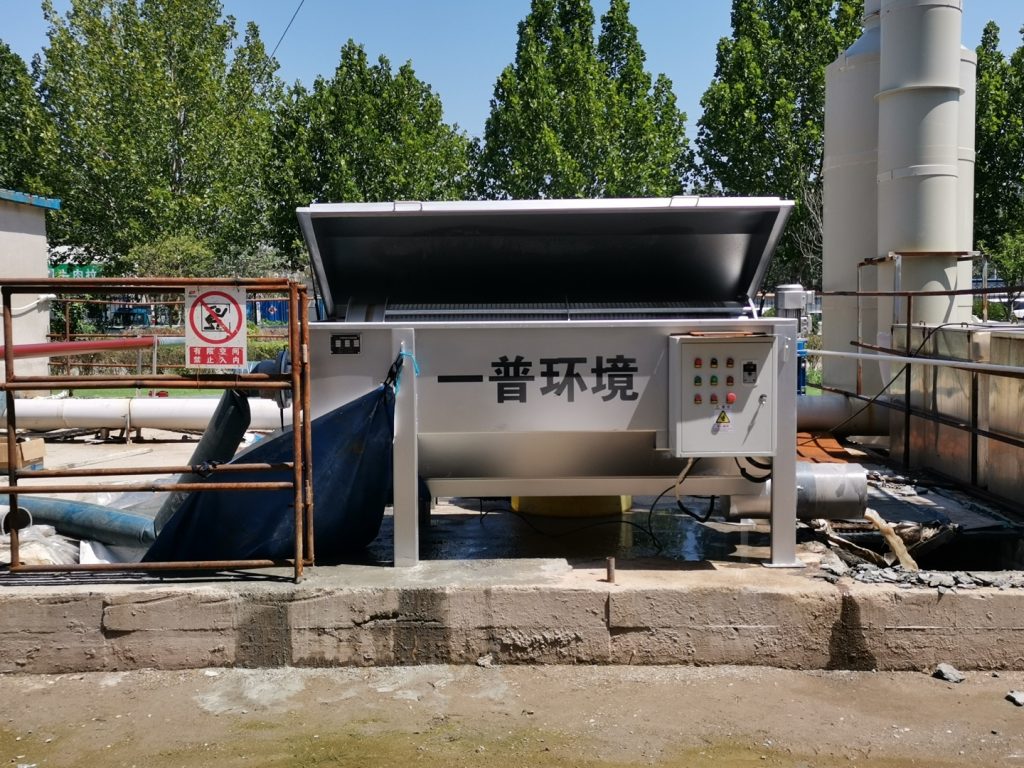
Water quality changes
1.COD: The amount of COD generated in the bleaching wastewater of pulp is 40-85 kg/t of product, and its value depends on the kappa number of unbleached pulp. According to the “Best Available Techniques (BAT) Reference Document for the Pulp and Paper Industry” of the European Union, if the kappa number obtained by cooking or oxygen delignification is reduced by one unit, the COD released in the bleaching equipment will be reduced by about 2 kg/t of product. Compared with traditional elemental chlorine bleaching, the COD load of bleaching wastewater will decrease as the substitution of chlorine with chlorine dioxide increases. When using chlorine dioxide bleaching instead of elemental chlorine bleaching, the COD load of wastewater can be reduced by 20%-25%. The use of oxygen delignification can also reduce the COD load of bleaching wastewater, usually by 40%-50%.
2.BOD: In the bleaching process, the residual lignin and the substitution rate of chlorine dioxide in the bleaching process have little effect on the BOD. If oxygen delignification is used for pretreatment before the bleaching process, the amount of BOD can be reduced. It has been reported that it can be reduced by 70%. The amount of BOD in bleaching wastewater is 10-30 kg/t pulp.
3.AOX: Lignin in pulp is the source of AOX in bleaching wastewater. Delayed delignification and oxygen delignification pretreatment can greatly reduce the kappa number of the pulp to be bleached, thereby reducing AOX in the bleaching wastewater. The AOX load of the bleaching wastewater decreases linearly with the increase of the substitution rate of chlorine dioxide in the chlorination stage. The formation of AOX is complex and depends on the type of bleaching agent, the distribution of available chlorine in each bleaching stage, and the form of chlorine addition in the bleaching process. Reducing the amount of available chlorine and adopting a stepwise addition of the bleaching process can reduce the AOX load in the bleaching wastewater. According to statistics, the amount of AOX generated by the bleached straw pulp plant in a single-stage bleaching with sodium hypochlorite is between 2.4-7.8 kg/t of pulp, and the amount of AOX generated by the CEH traditional three-stage bleached straw pulp plant is 7.5 kg/t of pulp. The amount of AOX generated by the CEH reed pulp plant is 2.5-7 kg/t of pulp, the amount of AOX generated by the wood pulp plant is 4-5 kg/t of pulp, and the amount of AOX generated by the OHH three-stage bleaching is 1.5 kg/t of pulp. In recent years, the EU and other countries have adopted low-chlorine or chlorine-free bleaching processes, and the AOX emissions have been greatly reduced. The amount of AOX generated by most companies is less than 1 kg/t of pulp. The AOX level can be easily reduced to below 0.3 kgAOX/ADT by using ECF bleaching, and TCF bleaching almost does not generate AOX.Overflow water generated in various stages of pulping: if measured by COD, the organic matter content discharged in the overflow liquid is usually between 5-20 kg per ton of pulp.
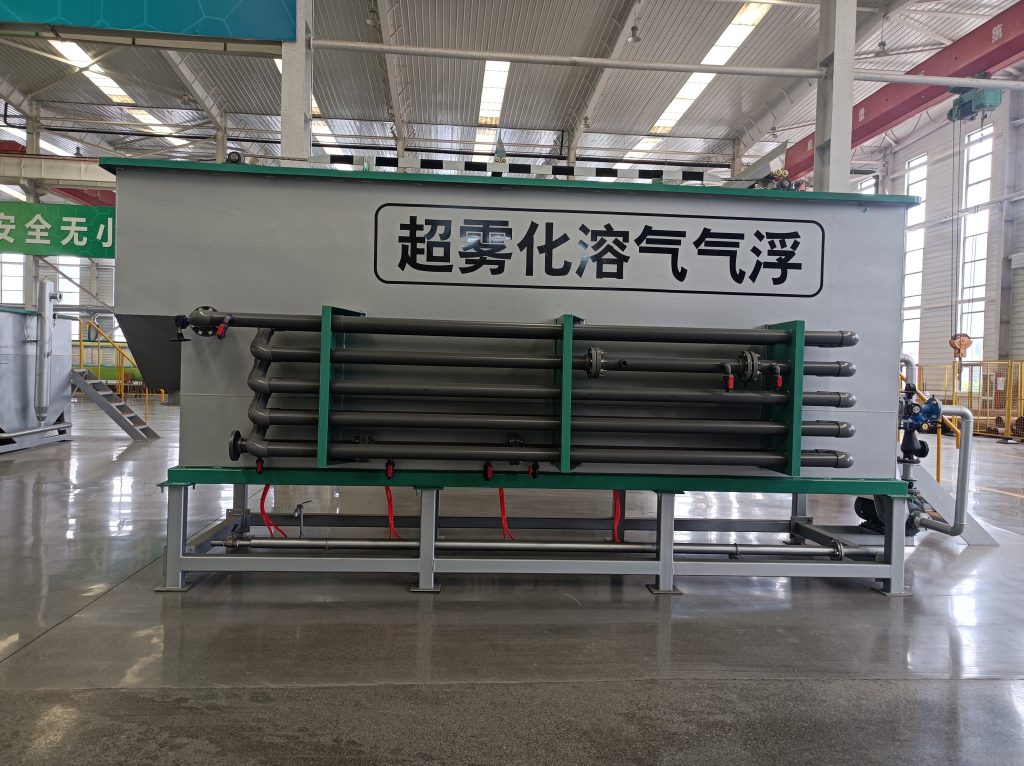
Papermaking Sewage Treatment Processes
一、Coagulation and Precipitation Method
The coagulation and precipitation method is characterized by simple technology, easy operation and management, high COD removal rate, avoidance of secondary pollution, low cost, and good treatment effect, and has good economic and environmental benefits. Precipitation is the preferred primary treatment method for paper mills, and this method can remove at least 85% of SS on average. The design parameters for primary sedimentation are an average SS removal rate of 75% to 85%. Common inorganic coagulants for recycled paper wastewater include aluminum sulfate, ferric chloride, ferrous sulfate, polyaluminum chloride (PAC), and so on, while organic coagulants include polyacrylamide (PAM), sodium alginate, and these organic coagulants are often used in combination with inorganic coagulants as coagulation aids. Under the most suitable conditions, the COD removal rate of coagulation and precipitation can reach 45%, and the turbidity removal rate can reach 95%. New coagulants, such as chitosan composite water purifiers, poly DADMAC, and aluminum chloride natural polymer composite coagulants, are also effective in removing COD and SS from wastewater.
二、 Air Flotation Method
The air flotation method is suitable for the treatment of wastewater containing a large number of small particulate matter with a relative density close to that of water. The principle of air flotation is to pressurize and inflate the wastewater and then reduce the pressure to remove suspended solids as they rise with the bubbles. Currently, high-efficiency shallow air flotation has become the mainstream of air flotation purification technology. This technology has a slightly higher removal rate of SS and COD than the precipitation method, and the obtained bubbles are very small and have a high density, which can reduce the addition of coagulants and reduce operating costs. Therefore, it exhibits certain advantages in small and medium-sized wastewater treatment.
After wastewater is treated by coagulation and precipitation or air flotation, high molecular COD substances, SS, and color are effectively removed. The COD load in the water mainly comes from dissolved, low-molecular-weight organic matter. Biological treatment can remove lower molecular weight organic matter, making up for the shortcomings of coagulation and precipitation. Studies have shown that after primary treatment by coagulation and sedimentation, the BOD/COD of wastewater from papermaking wastewater from waste paper is almost within 0.5-0.7, which is suitable for biological treatment.
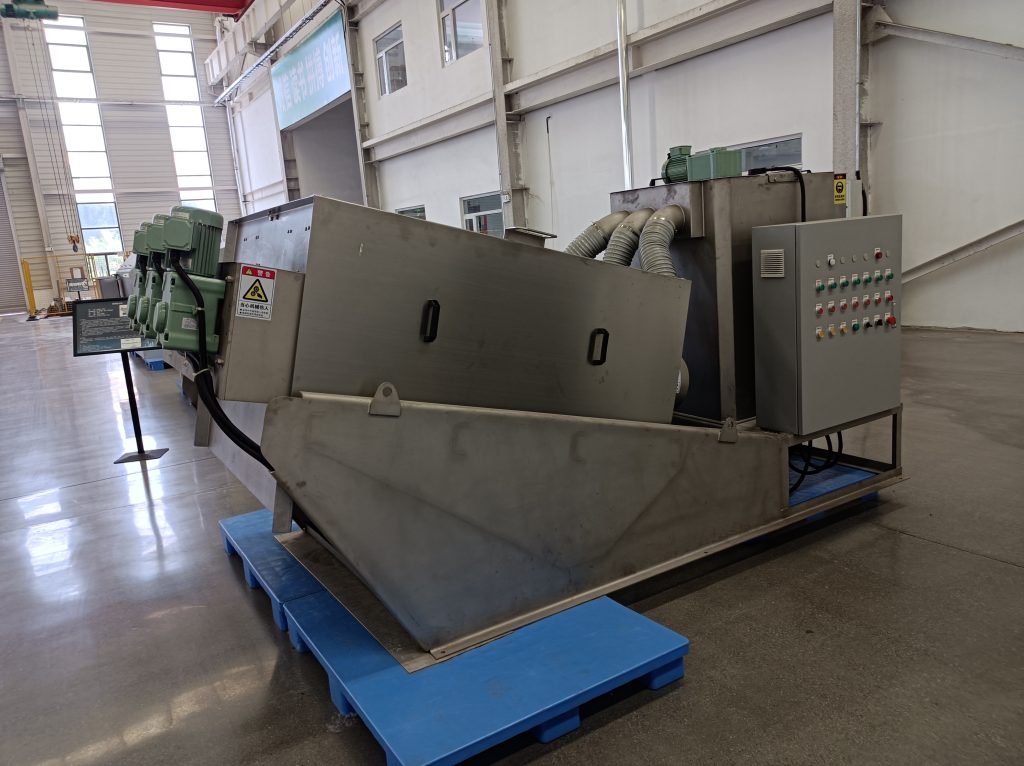
三、Advanced Oxidation Technologies
3.1 Biological Treatment Technologies: Biological treatment is the main process for treating papermaking wastewater, with various forms such as anaerobic biological treatment, aerobic biological treatment, and anaerobic-aerobic combined treatment.
3.2 Anaerobic Biological Treatment: Common anaerobic technologies include anaerobic baffled reactor (ABR), internal circulating anaerobic reactor (IC), up-flow anaerobic sludge bed (UASB), expanded granular sludge bed (EGSB), and other forms. In a project to treat papermaking wastewater in Henan, China, the IC process was adopted and proved to be able to adapt well to the fluctuation of influent quality and quantity, with a COD removal rate of 80%, a biogas production rate of about 0.38 m3/kg, and a biogas generation capacity of about 7,500 kWh/d, achieving a balance of the entire wastewater treatment system. Anaerobic granular activated carbon can remove 50% of COD. Using UASB reactor with a hydraulic retention time of 7 hours, COD removal rate can reach 66%. However, residual organic matter concentration in anaerobic effluent is often relatively high. Although the COD removal rate can reach 80% when using anaerobic treatment to treat papermaking wastewater, the COD residual concentration is still as high as 800 mg/L, so subsequent treatment is needed.
3.3 Aerobic Biological Treatment: Aerobic biological technology includes traditional activated sludge process, oxidation pond, and biological membrane process. Chandra pointed out that microorganisms in activated sludge, such as Pseudomonas, Citrobacter, and E. coli, can effectively remove BOD, COD, color, phenolic substances, and sulfides from wastewater. Junna also pointed out that the activated sludge process can remove 90% of BOD, 70% of COD, 60% to 95% of chlorophenols, and 40% to 60% of AOX. A paper mill in Guangxi, China, adopted the Tushan environmental protection activated sludge main process, with SS removal rate reaching 99.7%, COD removal rate reaching 98.4%, stable operation, and effluent meeting the discharge standard. In addition, the activated sludge process has a high removal effect on toxic substances in wastewater.
In addition to the traditional activated sludge process, using oxidation pond technology to treat papermaking wastewater, the COD removal rate of the engineering-scale oxidation pond is 30% to 40%, while the pilot-scale oxidation pond can achieve a COD removal rate of 60% to 70%. The BOD7 removal rate of the aerobic pond is 50% to 70%, and the chlorophenol removal rate is 10% to 50%. Using an aerobic pond to treat papermaking wastewater in Hebei, China, the removal rates of SS, BOD7, COD, and color were 85%, 95%, 68%, and 26%, respectively. In addition, the AOX removal rate in a short retention time treatment system of oxidation pond treatment of papermaking wastewater can reach 75%. Compared with the activated sludge process, the biological membrane process can more effectively remove difficult-to-degrade toxic and harmful substances, and has a smaller footprint, less sludge production, stronger processing capacity, and can adapt to the impact load of water quality and quantity changes, which is more practical for wastewater treatment of small and medium-sized enterprises. The biological membrane process technology takes various forms, including SBR biofilm reactors, high-density biological reactors, and biological filters.
3.4 Anaerobic-aerobic combination technology: Although the recycled paper wastewater treated by coagulation and sedimentation is suitable for biochemical treatment, due to the variety and high concentration of pollutants, anaerobic-aerobic combination technology can achieve a more ideal removal effect. The purpose of anaerobic pretreatment is to reduce the concentration of organic matter, degrade refractory organic matter, improve the composition structure of organic matter in wastewater, and further improve the biodegradability of wastewater.
By using anaerobic and aerobic reactors in combination, the removal rates of BOD, COD, and fatty acids were 88% to 94%, 76% to 96%, and 85% to 95%, respectively. By using the pilot-scale IC-A/O biological treatment process to treat recycled paper wastewater, the removal rates of COD and SS were both 98%, and the color removal rate was 97%. In addition, the application of hydrolysis-acidification-CASS biological treatment process in a paper mill in Jiaozuo improved the biodegradability of wastewater to a large extent and improved the treatment efficiency of aerobic biochemical system. The subsequent removal of organic matter was concentrated in the CASS tank. The system operated reliably, and the performance was stable, with removal rates of 96.2% and 93.5% for SS and COD, respectively.
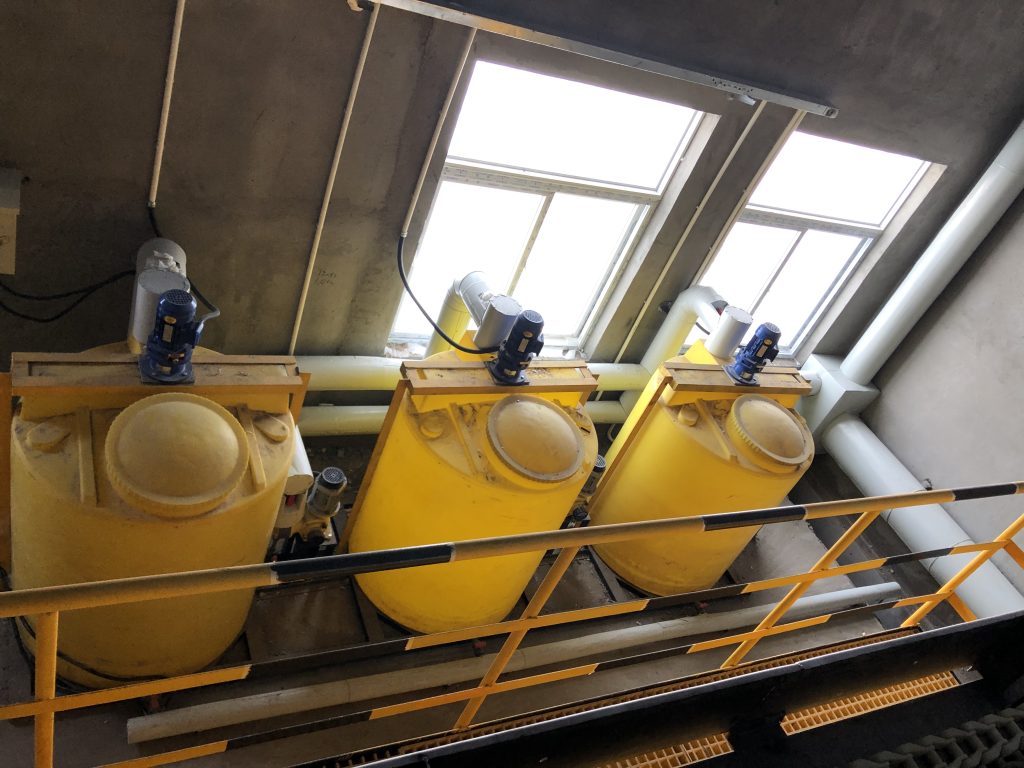
四、Adsorption method
The commonly used adsorbents in papermaking wastewater treatment include activated carbon and fly ash. It has been found that granular activated carbon (GAC) can effectively remove biologically refractory organic matter in biochemical effluent, and the molecular weight and aromatic compound content of pollutants in wastewater are the key factors affecting the treatment effect of GAC. In addition, using the bottom ash of power plant waste as an adsorbent has also achieved good treatment effects, and the higher the organic carbon content and the smaller the particle size of the bottom ash particles, the better the adsorption effect on organic pollutants.
五、 Combinatorial chemical oxidation process
There are many combined treatment methods for papermaking wastewater, including the use of ozone oxidation and fixed-bed biofilm reactor technology to improve the water quality of discharged wastewater. Fenton reagent and ozone are commonly used oxidants. The use of Fenton reagent in pilot-scale treatment of biochemical effluent shows that the COD removal rate exceeds 92%. Ozone oxidation was used for deep treatment of papermaking wastewater, and the COD removal rate reached 68%. Ozone was used as a tertiary treatment process, which can remove 85% to 95% of COD and 96% of BOD. This process has a good effect on the removal of COD, chromaticity, and AOX, and requires less ozone. The research results of the chemical coagulation, air flotation, and biological contact oxidation process for treating wastewater from recycled paper production show that the process can increase the reuse rate of the middle section water to 85%. High-dose ozone treatment of papermaking wastewater for 18 minutes can achieve a chromaticity removal rate of 98%. In addition, after ozone treatment, not only the COD and TOC content and toxicity of papermaking wastewater were significantly reduced, but the biodegradability was also improved.
六、 Membrane filtration
Membrane treatment technology is mainly used for the treatment of papermaking wastewater with microfiltration and ultrafiltration technology. Membrane separation technology can effectively remove COD, chromaticity, and AOX in papermaking wastewater. Experimental and case studies have shown that ultrafiltration technology can achieve removal rates of 59%, 87%, and 99% for TOC, chromaticity, and SS, respectively, and the subsequent addition of dissolved air flotation technology can further improve the removal efficiency of TOC. A paper mill in Hunan Province, China, uses microfiltration technology, which can remove more than 95% of SS and more than 88% of COD, and the effluent meets the standard and operates stably.
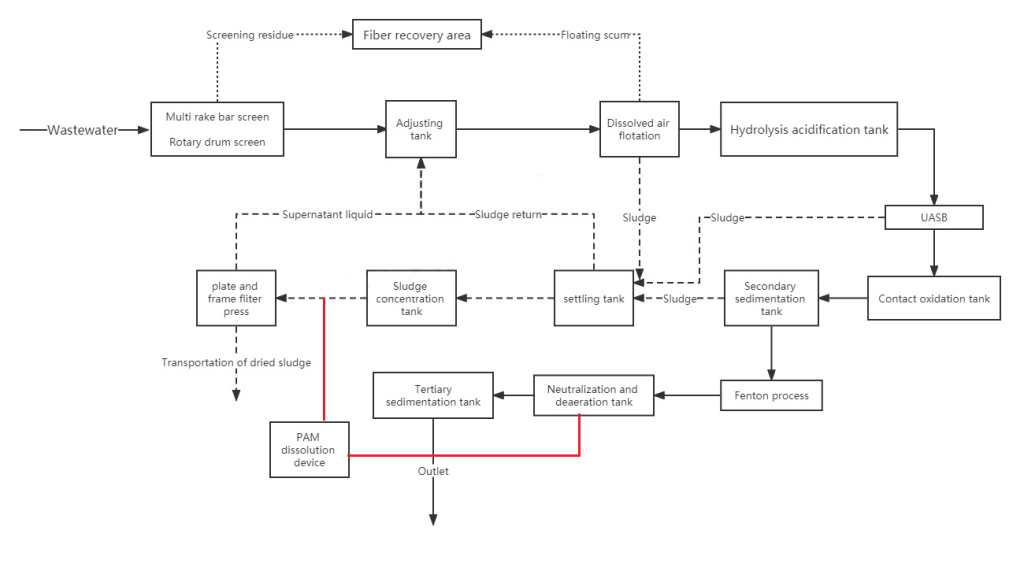