10 treatment processes for oily wastewater!
一、Definition of oily wastewater
Oily wastewater refers to wastewater that contains fats (fatty acids, soaps, fats, waxes, etc.) and various types of oils (mineral oils, animal and vegetable oils). Oily wastewater is characterized by high levels of chemical oxygen demand (COD) and biochemical oxygen demand (BOD), a certain odor and color, flammability, easy oxidation and decomposition. Generally, it is lighter than water and insoluble in water. Oily wastewater is a large-scale and seriously hazardous industrial wastewater. Its pollution is mainly manifested in the following aspects:
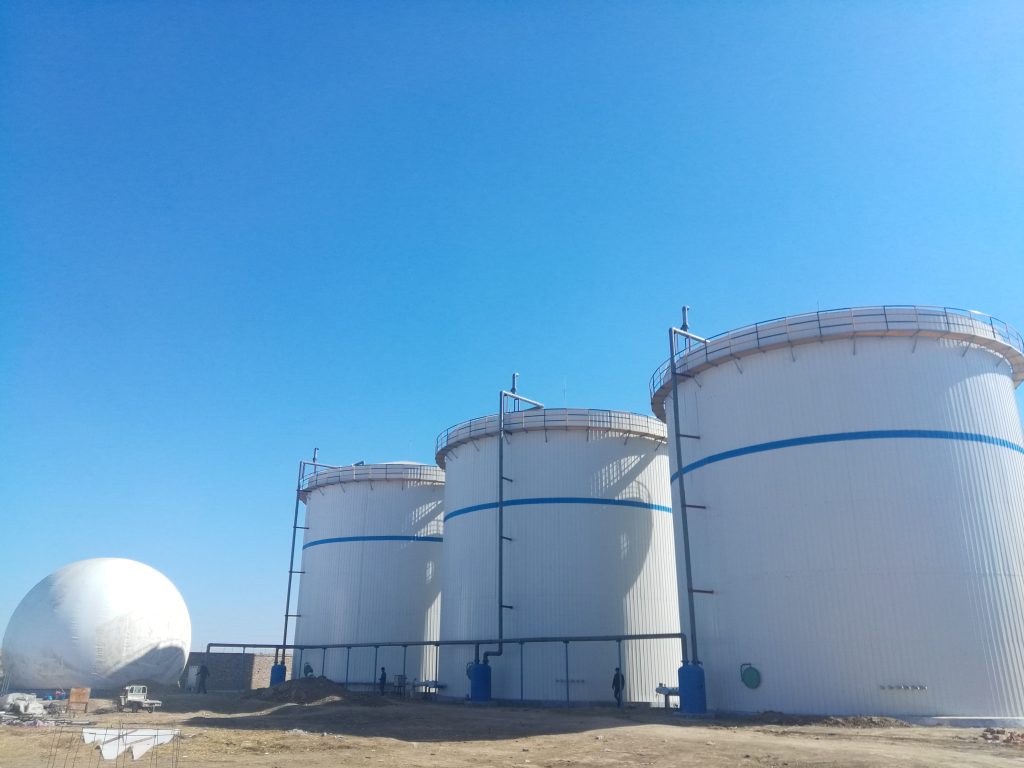
- Deterioration of water quality and harm to aquatic resources.
- Harm to human health.
- Air pollution.
- Impact on crop production.
- Impact on natural landscapes.
- Impact on clean natural water sources.
- Considering the pollution caused by oily wastewater, China has set the maximum allowable discharge concentration of oily wastewater at 1 mg/L.
二、Forms of oil in water
- Suspended oil: Particles with a size of ≥100μm that can quickly rise to the surface when left undisturbed, forming a continuous oil film floating on the water surface.
- Dispersed oil: Particles with a size of 10-100μm that are suspended and dispersed in the water. With sufficient time for settling or the action of external forces, they can coalesce into larger oil droplets that rise to the water surface. They may also further reduce in size and transform into emulsified oil.
- Emulsified oil: Particles with a size of 0.1-10μm (extremely fine oil droplets) that are stably dispersed in water in the form of water-in-oil emulsion due to the influence of surfactants at the oil-water interface. Achieving oil-water separation solely through settling is challenging.
In typical oily wastewater, not all three forms of oil mentioned above may be present. However, in representative industries such as electroplating wastewater, all three forms exist, with the highest proportion attributed to emulsified oil. The concentration of grease in general oily wastewater is usually around 300-500 mg/L.
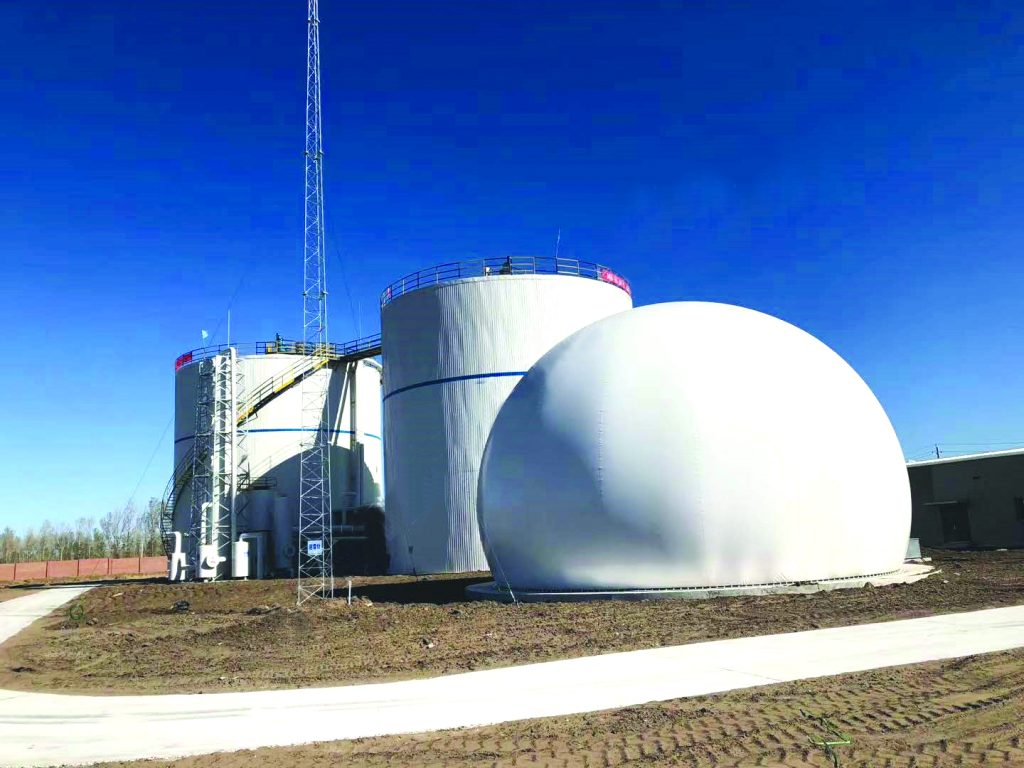
三、10 Common Methods for Treating Oily Wastewater:
- Sedimentation Separation Method:
The sedimentation separation method utilizes the density difference between oil and water, as well as their immiscibility, to achieve separation. It is a primary treatment method. Sedimentation separation is conducted in an oil-water separator, which can take various forms such as concurrent flow, parallel plate, and corrugated plate separators. The design of concurrent flow oil-water separators is primarily based on the Stokes’ law, which can determine the minimum oil droplet size that can be removed by a separator with a specific surface area. The flow condition in the oil-water separator significantly affects the oil removal capacity and efficiency. The ideal flow condition is laminar flow, as it facilitates the rise of oil droplets and the settling of solid particles.
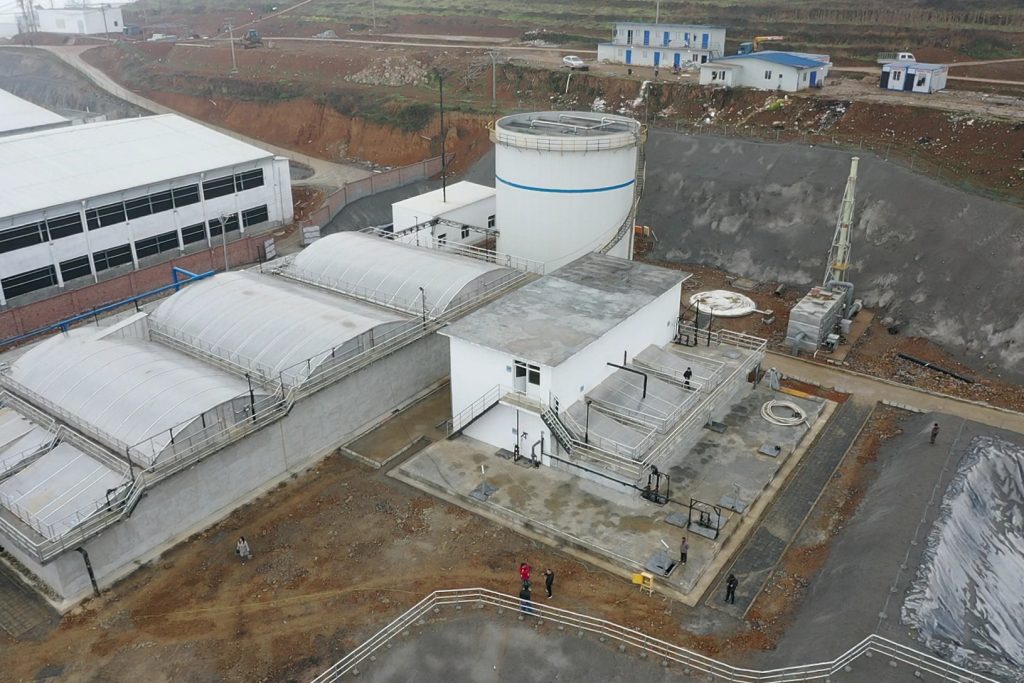
2. Coagulation Method:
The coagulation method separates oil and water based on the differential affinity of the two phases for coagulation materials. When oily wastewater passes through coagulation materials, the smaller oil droplets coalesce into larger oil particles, thereby increasing their buoyancy. This method belongs to the secondary treatment.
The coagulation method involves filling the coagulation materials into a coagulation device, which can remove dispersed oil from the wastewater. The key to this technique lies in the choice of coagulation materials, which can be in the form of fibers or granules. Common hydrophilic materials include polyamide, polyvinyl alcohol, and viscose fibers, which are modified with acidic groups (sulfonic acid, phosphoric acid, etc.) and salts. Hydrophobic materials, on the other hand, include wax beads, polyolefin or polystyrene beads, and polyurethane foams. It is generally considered favorable if the contact angle is less than 7°.
The effectiveness and feasibility of oil removal are determined by changes in oil droplet size distribution before and after coagulation. The main evaluation parameters are oil removal efficiency and oil content in the effluent.
The coagulation method does not require additional chemicals, avoids secondary pollution, requires less space for equipment installation, and has lower infrastructure costs. However, it requires a low inlet concentration of oily wastewater. Therefore, pretreatment of the oily wastewater prior to entering the equipment is necessary; otherwise, the oil concentration in the effluent will be relatively high (typically higher than 10 mg/L), requiring further treatment.
3. Filtration Method:
The filtration method uses a granular medium bed to trap oil in water through mechanisms such as inertial collision, sieving, surface adhesion, and coalescence. It is generally used for secondary treatment or advanced treatment. Common granular filter media include quartz sand, anthracite coal, glass fiber, and high molecular weight polymers.
In one locomotive factory, for example, oily wastewater undergoes oil-water separation, coagulation, sedimentation, and then filtration. The effluent meets all the required discharge standards, with an oil removal efficiency of up to 95%. It can be directly used in the related production workshop.
Filtration methods have the advantages of simple equipment, convenient operation, and low investment costs. However, as operation time increases, the pressure drop gradually increases, requiring frequent backwashing to ensure normal operation.
4. Membrane Separation Method:
The membrane separation method, pioneered by S. Sourirajan, has rapidly developed over the past 20 years as a separation technique. In the treatment of oily wastewater, the membrane separation method utilizes porous membranes as the separation medium to retain oil and surfactants in the wastewater while allowing water molecules to pass through, achieving the goal of oil-water separation. The key to membrane separation technology lies in the selection of membranes and components.
Membrane materials can be classified into polymeric membranes and inorganic membranes. Common polymeric membranes include cellulose acetate membranes, polysulfone membranes, polypropylene membranes, and polyvinylidene fluoride membranes. Common inorganic membrane materials include alumina, zirconia, and titanium oxide. They can be further categorized into microfiltration, ultrafiltration, and reverse osmosis based on pore size. This method is most suitable for treating oily wastewater with high discharge requirements but relatively low treatment capacity.
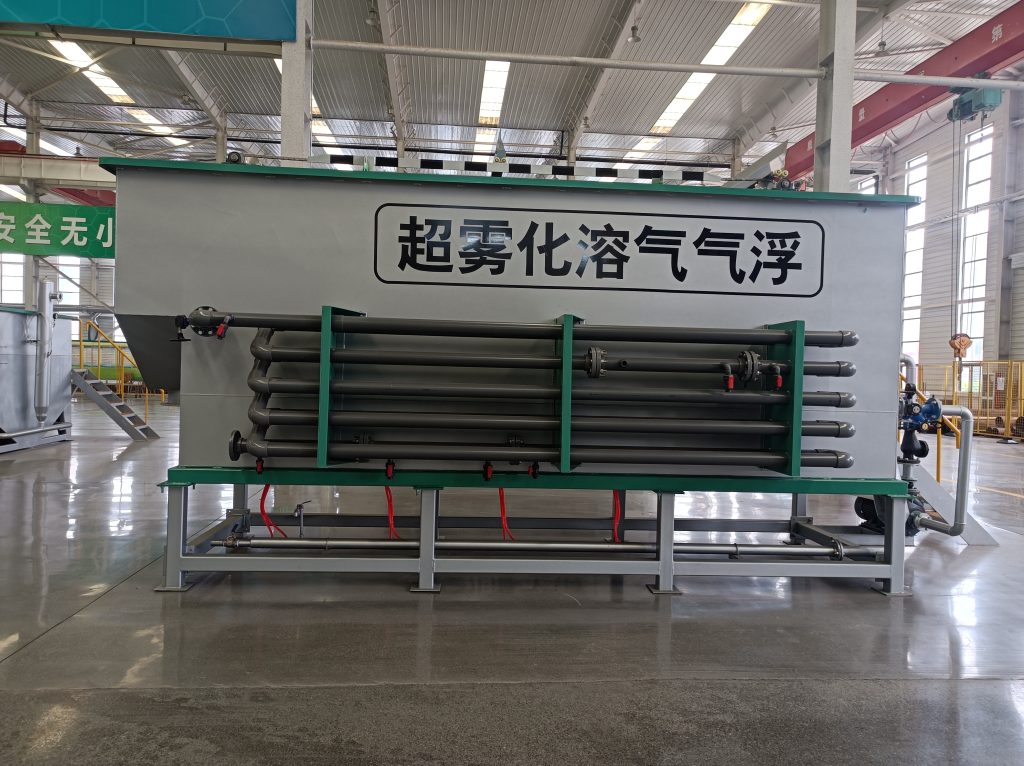
5. Flotation Method:
The flotation method relies on microbubbles adhering to oil droplets in water to increase buoyancy and achieve separation. It is mainly used to treat dispersed oil, emulsified oil, and fine suspended solids in oily wastewater that are difficult to remove by natural gravity separation (inorganic or organic coagulants are required).
Since the microbubbles are composed of nonpolar molecules, they can combine with water-based oil and rise together, significantly increasing the upward velocity and achieving high efficiency in oil-water separation. Depending on the method of bubble generation, the flotation method can be classified into pressure dissolved air flotation, impeller flotation, and air flotation.
To improve the flotation efficiency, inorganic or organic high-molecular-weight coagulants can be added to the wastewater, known as coagulation flotation, which further enhances the oil-water separation effect. This method has been widely applied in the treatment of oilfield wastewater, petrochemical wastewater, and edible oil production wastewater, and the technology is relatively mature.
6. Adsorption Method:
The adsorption method utilizes porous solid adsorbents to surface adsorb dissolved oil and other soluble organic substances in oily wastewater. Activated carbon is a commonly used adsorbent, which not only exhibits good adsorption performance for oil but also effectively adsorbs other organic compounds in wastewater. However, the adsorption capacity is limited (generally around 30-80 mg/g for oil), and it has high cost and difficulties in regeneration, limiting its application.
After treatment by the adsorption method, the oil content in the effluent can be reduced to below 5 mg/L. Therefore, the adsorption method is generally used for the advanced treatment of oily wastewater. In the treatment of oily wastewater from shipbreaking yards, for example, the oil content in the effluent is below 5 mg/L, with most values below 1 mg/L. The adsorbents used include modified bentonite, sulfonated coal, spent activated carbon, coke fines, and organic fibers, which are readily available materials.
7. Coagulation Method:
The coagulation method involves adding a certain proportion of coagulants to the wastewater to generate hydrophobic flocs, which adsorb micro oil droplets, followed by oil removal through sedimentation or flotation.
Common inorganic coagulants include aluminum sulfate, ferrous sulfate, ferric chloride, polyaluminum chloride, and polyaluminum chloride. Organic coagulants such as polyacrylamide and acrylamide polymers are also commonly used. The pH range for different coagulants varies.
To enhance the coagulation effect, often two coagulants are used in combination. This method requires a large dosage of coagulants and generates a significant amount of sludge, making it suitable for treating large volumes of wastewater with relatively low oil content, such as emulsified oils or other fine suspended solids.
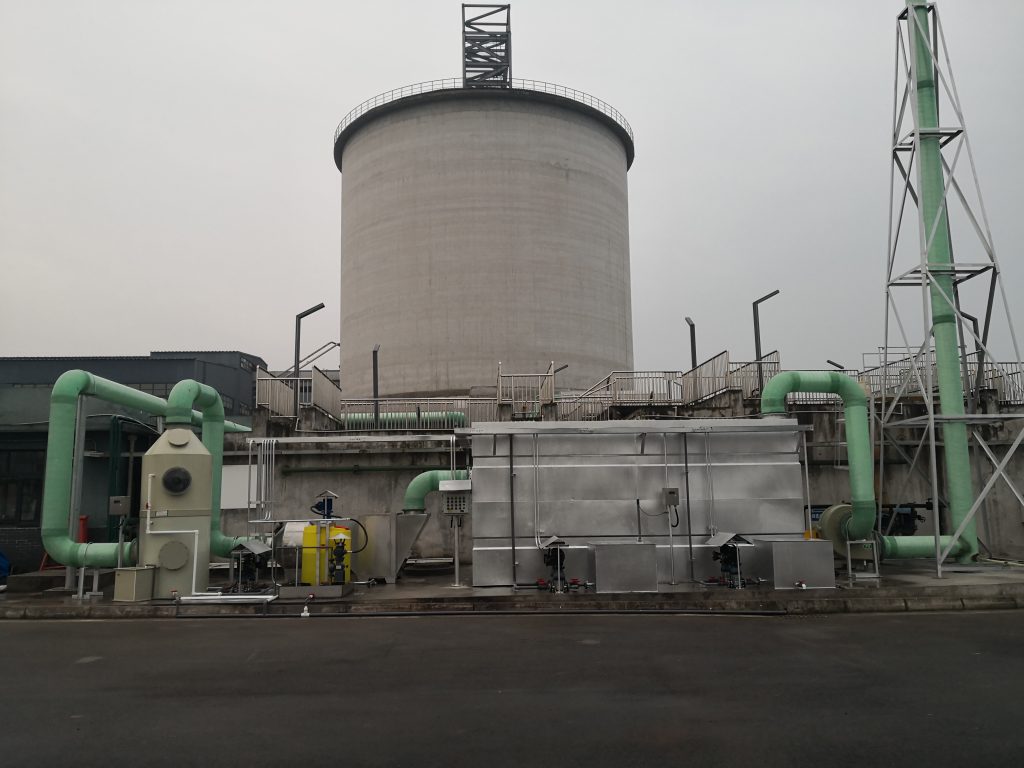
8. Salt Precipitation Method
The salt precipitation method involves adding inorganic salt electrolytes to the wastewater. The electrolytes cause the cations in the oil droplet diffusion layer to be displaced into the adsorption layer, disrupting the double layer and neutralizing the oil droplets. As a result, the attractive forces between the oil droplets are restored, leading to coalescence and achieving the demulsification purpose.
Commonly used electrolytes are salts of calcium, magnesium, and aluminum. They can both neutralize the charges and alter the properties of surfactants, thereby improving the treatment efficiency. The dosage of salts in the salt precipitation method is generally between 1% and 5%. After treatment with this method, the oil content in the effluent is typically higher than 10 mg/L. However, this method has a slow coalescence rate, long settling time, and requires a large footprint for equipment. Moreover, it is not effective for treating oil-in-water emulsions stabilized by surfactants.
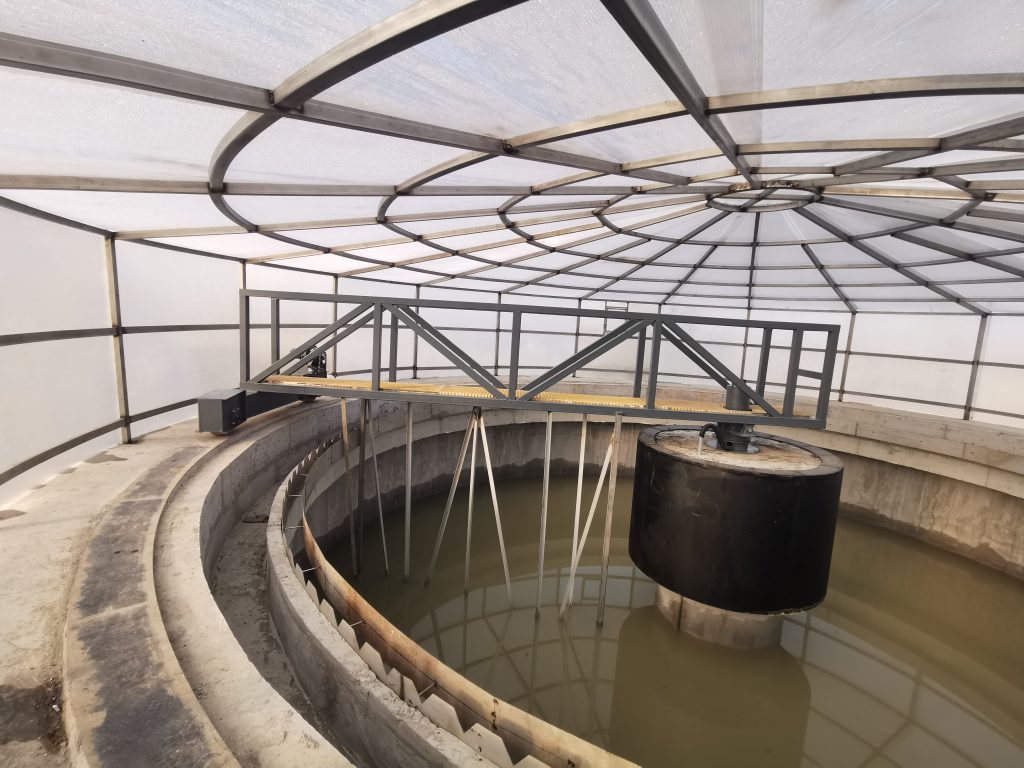
9. Electrolytic Method
The electrolytic method includes electrolytic coagulation adsorption and electrolytic flotation. Electrolytic coagulation adsorption involves the electrolysis of emulsified oil wastewater. Metal ions are dissolved from a soluble anode (Fe or Al), and these metal ions undergo hydrolysis to form hydroxide species that adsorb and coagulate emulsified oil and dissolved oil, which can then be separated by settling.
This method is mainly suitable for the secondary treatment of cooling and lubricating fluids in machining industries after chemical coagulation. Electrolytic coagulation adsorption has advantages such as a small footprint, simple operation, good treatment efficiency, and relatively low sludge production. However, it has drawbacks such as high consumption of anode metals, the need for a large amount of salts as auxiliary agents, high power consumption, and high operating costs. In addition, although research on anode passivation issues has been conducted extensively, it has not been fundamentally resolved yet.
10. Biological-Chemical Method
The biological-chemical method is highly effective in removing dissolved oils from water. However, it cannot remove dispersed oils and suspended oils. If the system contains these types of oils, it can significantly impact the entire biochemical system. Therefore, when applying the biological-chemical method to treat oily wastewater, proper pretreatment should be carried out to remove suspended oils and dispersed oils from the water.