Oil separation and treatment systems
In order to sell the liquid hydrocarbons that are produced by oil producing wells, they need to meet specifications that define the maximum allowable amount of water and salt, along with other impurities.
Unfortunately, the liquid hydrocarbons that are produced by the wells seldom (if ever) match these requirements. So, there will always be some necessary treatment of the oil required before it is ready to pass onwards into pipelines or other transportation systems.
The main function of an oil treatment train is to separate the oil, gas, water, and solids, and to treat the oil to meet custody transfer specifications (e.g, BS&W, salt content, vapor pressure).
This are typically achieved through the use of gravity, time, changes in pressure and temperature, and through the use of electrostatic fields.
In the oil field, the principal technologies used for oil treatment are Multi-phase separation, crude oil Dehydration, and crude oil Desalting, although there may also be heaters and other tanks used within the process train.
In the case of refineries, oil treatment is centered on the requirements of the crude unit where refinery desalting is undertaken as the first step of the refining process, and distillate treating, where refined products are treated to remove trace impurities from their make-up prior to storage and sale.
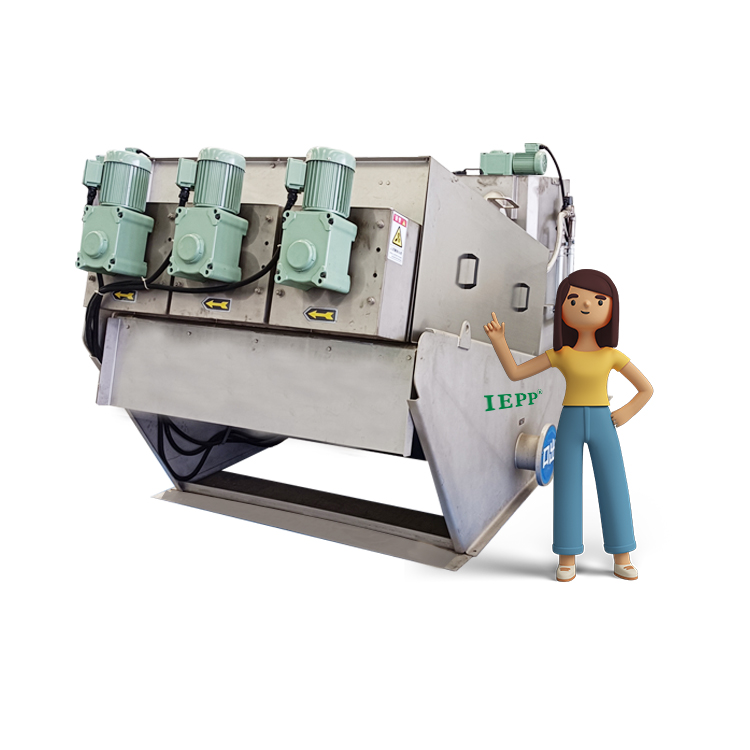
Multi-phase Separation
The gathered fluids from the well heads must be processed to enhance their value. First of all, fluids must be separated into their principal components – namely, oil, water, and natural gas. The multi-phase separation system performs this function.
The physical separation of these three phases is carried out in several steps. Water is separated first from the hydrocarbon mixture (typically by means of a Free Water Knock-Out (FWKO) vessel), and then the hydrocarbon mixture is separated into two hydrocarbon phases (gas and oil/condensate). A successful hydrocarbon separation treatment maximizes production of condensate or oil, and enhances its properties.
In field applications, this is accomplished by means of multi-stage separation. Multi-stage separation of oil and gas is carried out with a series of separators operating at consecutively reduced pressures. Liquid is discharged from a higher-pressure separator into the next-lower-pressure separator. The purpose of stage separation is to obtain maximum recovery of liquid hydrocarbons from the fluids coming from the wellheads and to provide maximum stabilization of both the liquid and gas effluents.
Usually it is most economical to use three to four stages of separation for the hydrocarbon mixture. Five or six may payout under favorable conditions, when, for example, the incoming wellhead fluid is produced at very high pressure. However, the increase in liquid yield with the addition of new stages is not linear.
In general, it has been found that a 3-stage separating system is normally the most cost effective
The detailed design of multi-phase separators can vary greatly, but they all follow some basic principles. The main function of a separator is the segregation of oil, water and/or gas within a single vessel.
Separators are used throughout the production and processing of crude oil and natural gas. From upstream (production) to downstream (oil refineries and gas plants) and all the way through transportation, separators are used to ensure a basic level of phase purity adequate for the corresponding processing stage is obtained.
Separators utilize gravity or other “G” forces to split the phases, and exactly how the phases are split will vary from application to application. Even though separators will only separate free liquids, and not liquids in the vapor state, they are the most common type of process equipment found in the oil and gas production facilities.
A single multi-phase stream will enter the separator vessel. The oil stream will contain most of the oil and some water (typically in the form of an emulsion, difficult to separate by gravity alone).
The water stream will contain most of the water and some oil (typically the smaller oil droplets dispersed in the water) and usually also flushes away from the vessel the separated solids.
The gas stream will essentially consist of gases and vapors forming a single phase and therefore the (phase) separator itself will not be able to separate them further.
There are a variety of different designs of multi-phase separators, with numerous different internals configurations, which will be selected based on the range of process conditions for a particular application.
Some internal components are more suited to mitigating foam generation, whilst others can maintain performance over a wide flow range.
But whatever the internals configuration, getting the operation of the separation stages correct is vital as any problems occurring at the front end of the process will cause downstream effects not only in the subsequent oil processing equipment, but also the gas processing and the water processing.
Field Operations & Treatment
Even after having been treated through a multi-stage separation train, the liquid hydrocarbons will still contain too much base sediment and water (BS&W), and they will need to undergo additional processing prior to being sold into a pipeline or other transportation system.
As such, the separated crude oil will normally need to undergo dehydration and/or desalting.
Dehydration of crude oil refers to the removal of dispersed (or insoluble) water. This water may originate with the production stream or may be introduced as ballast (during transportation) or as wash water in a crude oil desalting operation (where mineral salts are washed from the crude by mixing the crude oil with lower salinity water).
Dehydration is accomplished by providing an environment in which the dispersed water droplets can be separated through gravity separation. This process may be aided by allowing the droplets to grow via coalescence. This droplet separation can be enhanced through mechanical means (such as via the introduction of heat to reduce viscosity, or via the use of coalescing packing) or by chemical means (such as the use of emulsion breakers). When these methods are insufficient to achieve an economic separation down to the required level, then electrostatic treatment is used to accomplish the separation.
What are the reasons for performing crude oil dehydration?
One of the first concerns leading to the need for dehydration is the accounting for the oil moving from the production site into the buyer’s pipeline or transportation. This is followed closely by the desire to minimize corrosion in the tankage, pipeline, or transportation vessel.
In pipeline operations, water volume leads to unnecessary use of pump horsepower. Water tends to settle out of the moving stream in the pipeline and accumulate in low spots. As this accumulated water is pushed out of the low spots, slugs of water arriving at the delivery end cause processing difficulties in the receiving facilities.
Also, in both field operations in which elevated temperatures are required, the heat load produced by water in the oil results in significant fuel consumption. Dehydration provides a means of reducing this fuel consumption.
Dehydration requirements vary with the type of downstream processing, the climate of the production area, and the type of oil being produced. Here we take a look at the BS&W level that would typically be required for some applications.
For example, storage at the production site or shipping terminal requires less stringent water removal than transportation in a pipeline or ship which, in turn, are less demanding than refinery processing. Water removal in cold climates, where pipelines and storage facilities are subjected to extremely low temperatures, is more critical than in a warm climate. For practical reasons, oil that is very heavy or very high in difficult-to-remove solids may be subject to more lenient specifications than higher quality oils.
Saline water is more corrosive than fresh water, particularly if oxygen or other oxidizing agents are present. Such water causes corrosion in storage facilities and pipelines, and pipeline operators and shipping companies often impose restrictions on the amount of salt in the oil that they transport. Other salt in oil restrictions are imposed by the refineries and the amount of salt that can be tolerated in the refinery feed stock.
As such, it may be necessary to undertake desalting as part of the oil field upstream production operations
The desalting process consists of three steps: (1) the injection of the wash water into the wet oil, (2) mixing the wash water uniformly into the oil stream and generating drops of a size approximating those of the entrained water, and (3) resolution of the water dispersion in a desalter vessel.
Considerations regarding injection and mixing of the wash water will be discussed further, but the separation or dehydration step is the same three phase disengagement steps of coagulation, flocculation, and sedimentation.
Maximum allowable salt specifications vary, but some generalizations are possible. Requirements for treatment in the oilfield are usually expressed in two figures: (1) salt allowed in PTB (pounds of salt per thousand barrels of net oil), and (2) remnant water fraction allowed. For example, a specification might read:
Maximum salt content of desalted crude 25 ptb
Maximum remnant water in desalted crude 0.2%
It is also worth noting that low API gravity crudes typically have associated produced water which is less saline and thus mostly do not motivate crude field desalting.
Refinery Operations & Processing
Often by the time crude oil reaches the refinery it has not only been through “Field Dehydration” but maybe also “Field Desalting” to some level. This level may have been set by the transporter or by the refinery. In any case, it is usually not to a level acceptable for the protection of the refiner’s hardware or catalyst or perhaps even his end product. It must be desalted again to ensure that protection. Typical outlet requirements for a refinery desalting train might be less than one PTB salt and 0.1 or 0.2 percent residual water.
Operating conditions required to achieve these levels tend to be extreme compared to field desalting conditions. A typical refinery desalter might operate up to 300° F and at pressure commensurate with downstream processes; perhaps 150 – 300 PSIG, since the crude charge pump has to push the crude all the way through the fractionation tower.
The performance of a desalting system based solely on a salt removal may be expressed as an efficiency (a ratio of the amount of salt removed from the desalted crude to the amount in the incoming stream). However, salt removal efficiency is not a satisfactory way to measure desalter performance. For example, meeting 99% removal efficiency is quite reasonable with 100 PTB inlet salt, but is more difficult with 10 PTB inlet salt.
In refineries the salt problem becomes more troublesome. Due to higher processing temperatures and evaporation of entrained water in the distillation process, salt can produce fouling as well as corrosion in heating units and in the overhead sections. If salts reach the catalytic conversion processes, they can cause loss of catalyst activity due to reaction at the active sites on the catalyst as well as catalyst degradation as the salts attack the structure of the catalyst.
Since the anionic fractions of the salts accumulate with the heavier oil fractions, they can end up in the residual oils, asphalt, or coke products. The value of these products is then diminished.
Effective desalting systems allow the refinery to process a wider variety of feed stocks with smoother changeover between crude oils. Since some “slop oils” are re-processed by refineries, it is important that the desalting system is to handle some portion of these oils.
Once the hydrocarbons have been through the various refinery processes that produce the variety of end products (such as Kerosene, Diesel, and Naphtha), it still may be necessary to remove some trace contaminants from the end products that would impact their ultimate sales value.
Depending on the product it may be necessary to remove trace amounts of Sulfur, Nitrogen and Oxygen Compounds, water, naphthenic acids, chlorides, or other components. To achieve this may require the addition of certain aqueous reagents, which then will require removal. This includes Sulfuric acid and weak caustic solution.
Whilst the removal of the reacted contaminants is a dehydration process, unlike oil field dehydration, the bulk fluid is a refined and purified product which is non-conductive and cleaner. As such, different technologies can be used for the treatment of distillates that are leaving the refineries compared to the treatment of the crude oils that are entering them.
Summary
Whilst the merits of Oil Separation and Treatment Systems might be considered separate from the other process trains (Gas Treatment and Produced Water Treatment), all three systems really should be designed and operated as one production system, as the way that one system has been designed and is operated will have an impact on the other two.
There are many components within the oil that need to be evaluated when designing and operating an oil treatment system. Exactly how the system is designed and operated will determine if those components will or will not cause any issues in the oil treatment system or any of the other connected or downstream systems.