Solid-liquid separation in manure – how does it work?
Physical solid-liquid separation processes rely on the density, size, or shape of the individual particles. They usually involve settling by gravity, screening, or centrifugation. A basic requirement for the efficient separation of swine manure is the continuous agitation of the liquid that is processed. Otherwise, relatively fast sedimentation occurs that leads to reduced separation or inconsistent separation.
Settling (by gravity) is effective in waste water with less than one percent total solids. Settling can be very effective in removing small particle sizes. Settling is typically accomplished through a series of settling ponds or tanks. Gravity settling has been used for years and is the basis for using lagoons. The primary problem with settling is that the process is slow, can require several (3 or more) lagoons to be effective (therefore, has a large footprint), and the lagoons are often undersized for most operations, especially as growth of the operation occurs.
Screening is a process where the liquid manure passes through a screen. The solids are collected on the screen while the liquids pass through. The separation efficiency of a screening process depends on the size and design of the screen. Screens can be stationary, rotating, or vibrating. Stationary screens are mounted on an incline with the manure entering at the top edge of the screen. As the manure passes over the screen the liquids drain through the screen and the solids fall off the lower end. Vibrating screens are level with the manure stream entering the middle of the screen. The liquid passes through the screen openings and the solid portion vibrates to the edge of the screen and falls off. Rotating drum screens are designed to continuously rotate allowing liquid to pass through the screen and solids to move across the screen. This design keeps the screen holes open, because the screen is continually being scraped clean.
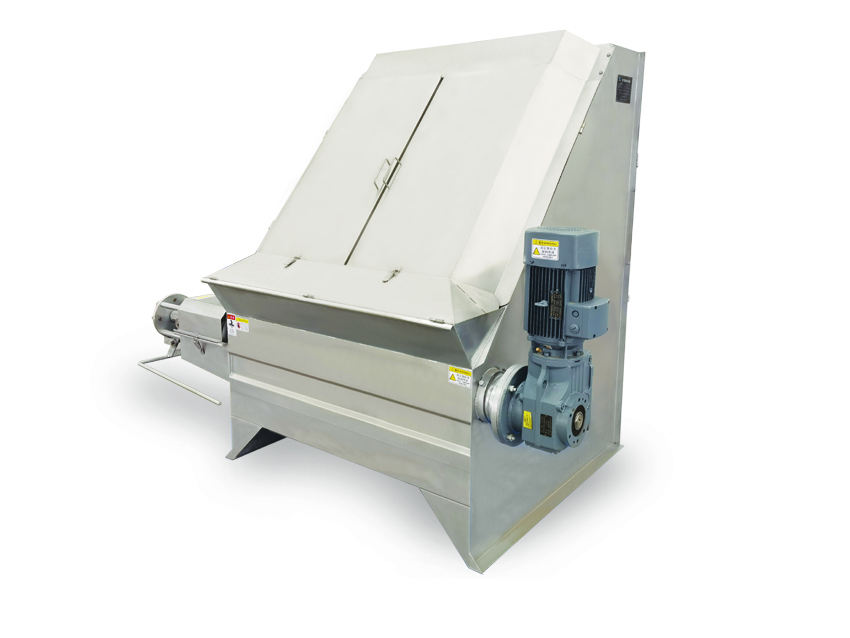
Other separators use smaller screen sizes and pressure to “squeeze” the manure through, e.g. screw press, belt press or centrifuge. These processes can handle manure with a higher solids content and are more efficient than typical screen separators but often require more capital investment and energy input.
Mechanical separators involve the collection of raw slurry in a large pit or storage tank. A large submersible or stationary bottom-impeller lift pump mixes the raw slurry and pumps it across a separator where the liquids drain off. Separators with few moving parts are most effective when large amounts of water are being moved through the separator. Mechanical separators can, in addition, use chemicals such as polymers and flocculants to separate solids from liquids. Mechanical separation is an effective treatment option for animal wastes, however, it is more costly and daily cleaning is required compared to gravity separation or sedimentation.
Screen separators usually receive manure that has been pumped from a collection pit. These types of separators can be installed above ground to allow for piling of separated solids. Piles of separated solids can be piled on a concrete pad with drainage either located in the back, in a manure spreader, or specialized container for additional processing. Screen separators typically only remove 25 percent of total solids, often referred to as separable solids. With a vibrating screen separator, liquid manure is pumped across a controlled vibrating screen. Liquid flushes through the screen while the solids are moved to the screen edge. The vibrating reduces clogging; however, powering requirements are greater than with a stationary inclined screen. A stationary screen separator has the liquid manure pumped to the top edge of the screen. Solids accumulate on the screen and move down while liquids move through the screen. This system requires no power (except for the pump needed to move the liquid manure) and limited moving parts. Unfortunately, with the stationary inclined screen solids build up occurs and clogs the openings. Therefore, frequent brushing or spraying with separated effluent or water is necessary for the holes to remain open. Rotating screens involve a screen continuously turning or rotating at a controlled rate. The liquid passes through the screen while the solids are scraped off the surface into a collection pit. Centrifuge separators function to dewater manure and rely on the differences of density between solid and liquid material. In general, centrifuge separators are more efficient in dewatering manure than other types of mechanical separators. Two types of centrifuge separators are centriseives and decanters also known as screw-presses. However, centrifuge separators function best with liquid slurries (<4% solids) compared to liquid waste (6 – 10% solids). These types of separators do not involve the use of chemicals (polymers or flocculants) to separate solids and liquids.
Belt filter presses are dewatering devices that involve the application of chemical conditioning, gravity drainage, and mechanically applied pressure to dewater liquid manure. The performance of belt filter presses depends on manure characteristics, method and type of chemical conditioning, pressure developed, machine configuration, belt porosity, belt speed, and belt width. Belt filter presses are effective in removing solids and liquids with low moisture content, however, the cost of operation and chemicals can be high. The main types of belt filter presses are roller and screw presses.
Roller presses include two concave screens and a series of brushes or rollers. The manure slurry is deposited on the first screen, moved across the two screens by brushes, and squeezed by rollers. The liquids are squeezed through the screens and the solids remain. Two types of roller presses are brushed screen with press-rolls and perforated pressure roller separators. The brushed screen with press-rolls uses a screen in the first stage and the solids are brushed onto the next stage. A roller is used to press the solids and the concentrated solids are brushed out of the separator. A perforated pressure roller separator is a two-stage double roller compression separator. For the first set of perforated rollers, liquid slurry is force-fed. Separated liquid is removed for storage at this point. Separated solids from stage one are conveyed to the second stage of rollers where fiber solids are removed by a mechanical conveyor. The liquid portion is drained off and returned to a tank.
Screw presses are composed of a screw-type conveyor in the center. The screw-type conveyor forces the manure slurry through a tube and past a cylindrical screen. Solids retained on the screen are pressed to the end and discharged. Rate of flow determines the solid removal from liquid manure. With most screw presses, the rate can be adjusted to control moisture content.
Gravity belt thickeners are a continuous belt thickener designed to increase the solid content up to 10 times. They consist of horizontal filter belts in which thickening takes place in two parts, gravity drainage and compression. Before the sludge is placed on the belt, it must be conditioned with chemical flocculent to form large stable flocs and a clear distinction between the separated solids and liquids (flocculation). The flocculated biosolids are placed on the continuous moving filtered belt and the water drains through. A series of ploughs are placed on the upper side of the belt to enhance gravity compression and assist in drainage. At the end, an inclined ramp is used to turn the biosolids against itself for further compression and water drainage. Gravity belt thickeners can increase dewatering capacity, reduce transportation and disposal costs, increase digester capacity, and reduce capital costs. In addition, they reduce space requirements, reduce operator and maintenance costs, and increase solids captured.
The use of chemical polymers and flocculants are frequently used to increase separation efficiency. Polymers and flocculants are used to alter the physical state of dissolved and suspended manure solids to increase the percent removed by solid separation equipment. Chemicals also, can be added to react with phosphorus and other metals to coagulate dissolved particles into small visible floc. The fine particles in liquid manure are referred to as suspended solids. Suspended solids contain proteins, soluble and insoluble carbohydrates, bacteria, and fine mineral (elemental) particles. Suspended solids, often referenced as total suspended solids (TSS) contain the odorous portion of the slurry. While solid-liquid separation processes do not necessarily reduce odor, often times the objectionable odor of liquid swine manure stays with the separated biosolids. If 90 percent or greater of the TSS is removed from raw slurry the resulting separated slurry generally has negligible odor.