Tips to ensure dissolved air flotation system success
Many industries must pretreat their process wastewater before discharging it to the local sewer system. Dissolved air flotation (DAF) systems are used to remove fats, oils, and grease (FOG), certain organics, suspended solids, and metals from process wastewater to meet sewer discharge permit requirements. These treatment systems are far more cost-effective than biological systems but can be ineffective and costly if they are not designed and operated properly.
The following tips will help ensure the success of DAF systems:
Design
An equalization tank is critical for balancing out fluctuations in influent pollutant loading.
Equalization tanks should be sized to hold a least one production shift’s flow.
Equalization tanks level should be allowed to fluctuate between 1/3 and 2/3 full.
Screening is important prior to the DAF tank to remove large solids that could damage pumps.
Hydraulic loading rates should be within the range of 2.0 – 5.0 gpm per square foot of flotation area.
Flocculation tubes provide better floc particle formation than flash mix tanks.
Air-handling pumps are the most efficient method for introducing dissolved air into the DAF tank.
The DAF unit should be designed to minimize short-circuiting of solids.
Sludge should be stored in a cone-bottom tank with air-agitation capabilities.
A plate-and-frame filter press is the most effective means for sludge dewatering.
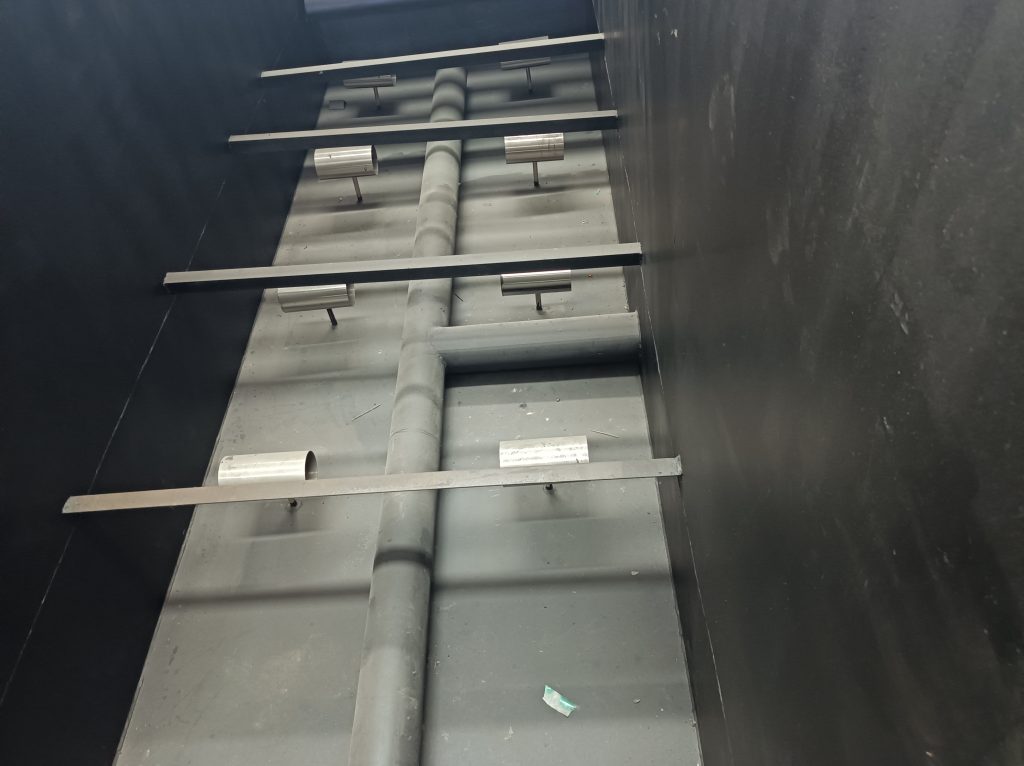
Treatment Chemicals
The most common treatment chemistry used is a cationic polymer (coagulant) followed by an anionic polymer (flocculent).
Clay is a cost-effective coagulant aid that absorbs FOG and organics and improves sludge dewatering.
Coagulant and clay need more mixing and retention time than the flocculent.
Chemical injection points should be angled in the direction of flow to prevent injection port clogging.
It is important to be able to observe floc formation in the flotation cell to ensure adequate treatment.
All chemical dosages must be determined through jar tests and not by “feel” or “operator instinct.”
Coagulant dosage will vary the most and can be automated with specialized instrumentation.
All treatment chemical feed pumps must be equipped with calibration columns for pump testing.
Operations
Sludge from the bottom of the DAF tank should never be recirculated back through the system; this will throw off chemical dosages and result in over-treated solids that pass through into the effluent.
The balance between air pressure, air flow rate, and recirculation flow is critical for effective flotation.
Moisture in compressed air lines will negatively impact flotation and filter press operation.
Frequent DAF start-ups and shutdowns will negatively impact effluent quality.
Solids collecting in the bottom of a DAF tank must be purged frequently to avoid pass-through to the effluent.
The float blanket should be 3 to 4 inches thick at the top of the DAF unit; less will result in watery sludge, while more may result in solids passing through to the effluent.
Recirculation pump pressure should be watched carefully as it can be used to predict maintenance needs.