Understanding dissolved air flotation (DAF)
A great way to deal with algae, fat, oil and grease (FOG) is to install a Dissolved Air Flotation (DAF). However, many face difficulties in operating the device and therefore, plant fails.
This article highlights some insights about DAF, how to select a proper DAF and what to do in order to have a good commissioning.
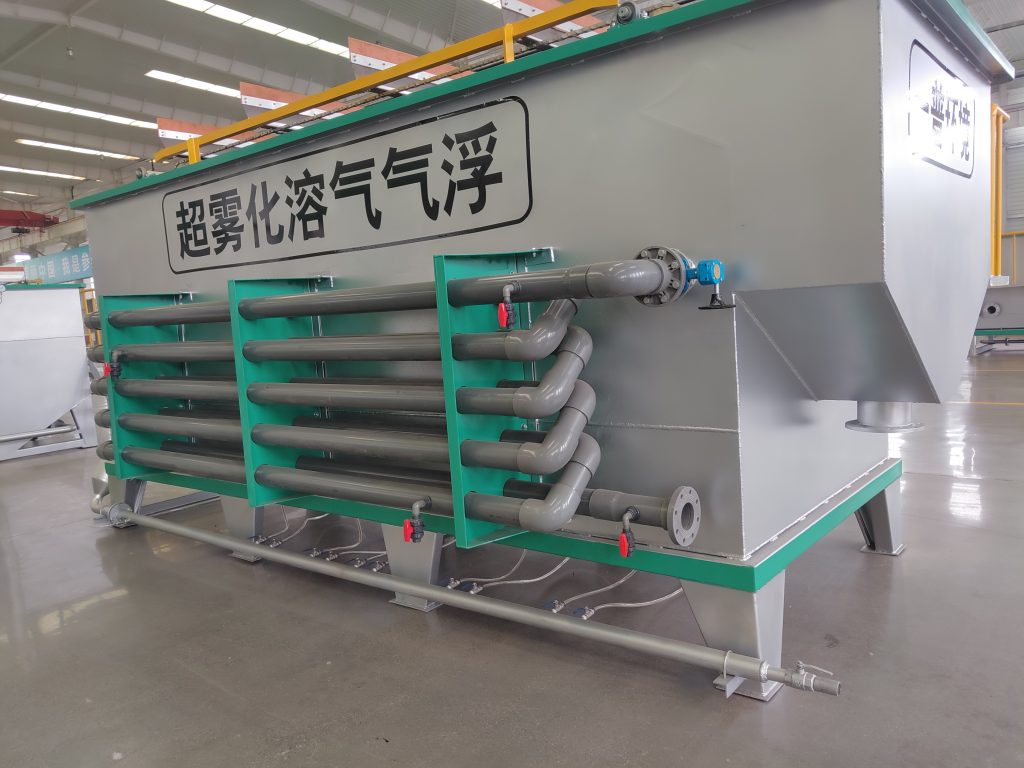
First of all, it is important to know which type of DAF are you integrating in your system; whether it is a gravity fed or pressure fed and act accordingly.
Next step is to know whether the DAF was designed with coagulation, flocculation tanks or it only comes as a flotation unit. Something to take care of prior integrating the designated DAF.
Third, it is important to know what is the level of FOG in your influent, if FOG is exceeding 500 mg/l, then DAF will not function properly.
Fourth, it is important to know what is the TSS particle size that is entering prior DAF. Typically, a 1 mm punch hole, bi-directional screen is a MUST. That is, since air bubbles are in between 10 – 100 micrometers, the process will not function if TSS entering is “bigger and denser/ disturb induced air” than induced air; therefore, it cannot float particles.
Fifth, it is important to cover the flotation tank to avoid wind disturbance to the process or any precipitants which might inhibit system.
Sixth, and this is a very crucial point, most of process engineers make mistake over here. Jar test! A proper jar test should be conducted to make a low particle charge and fairly hydrophobic. This means a small, low density floc that is easily to float. Many designers decide jar test results based on sedimentation not flotation! Then DAF will not work at all.
Cases of designing some elements of DAF:
In case of flocculation tank to be designed, a retention time will vary upon application, from 5 – 20 mins (maybe higher, based on what is the influent). In case of mixer selection, a higher flocculation energy is usually beneficial to develop a small, tough floc.
In case of designing baffling between the last stage of the flocculator and DAF inlet: it should be an over–under baffle arrangement, so that flocculated water flows downward and into the DAF basin at floor level, encouraging interaction between the flocculated water and the recycle stream.
Last note, water temperature, induced air temperature, pressure (elevation) should be known in order to correct design as needed. As known, air’s solubility in water is reduced at elevated temperatures.