What is coagulation and flocculation in water treatment?
Coagulation and flocculation are essential components of both drinking water and wastewater treatment. They provide a reliable process for treating water turbidity (the cloudiness or haziness of a fluid typically invisible to the naked eye), which is a key test of water quality. In wastewater treatment, they enable up to 90% reduction in suspended solids and organic loads.
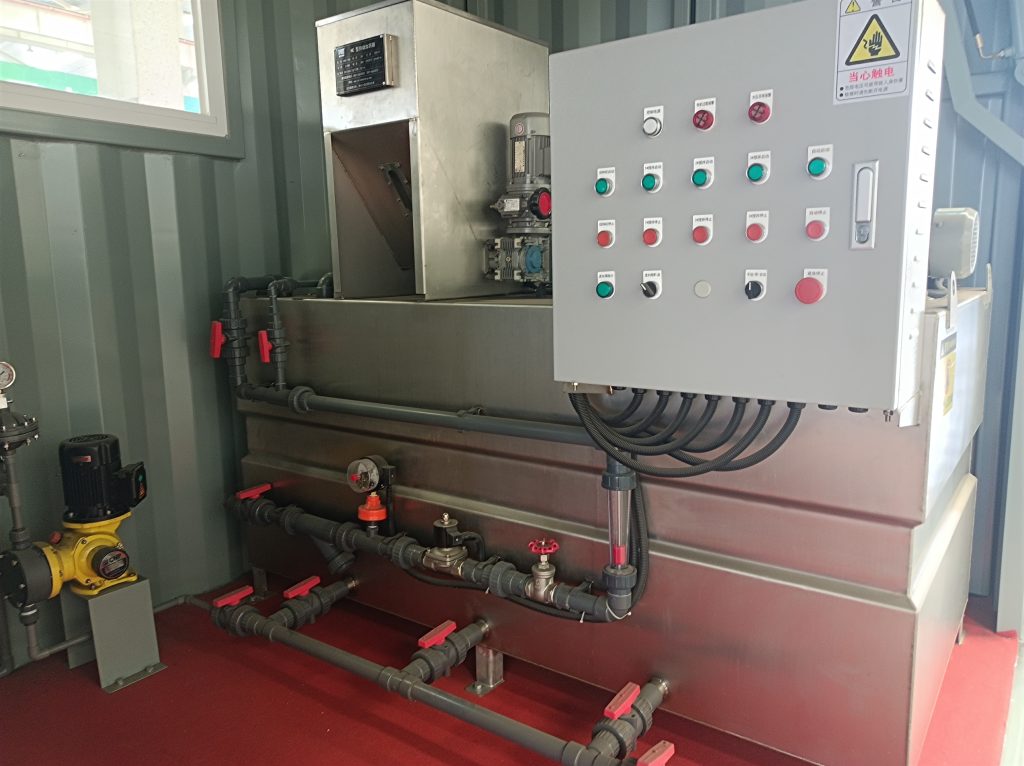
All waters contain suspended particles. The smallest particles (colloids) are stabilised by the action of physical forces (static electricity) on the particles themselves and, because they all have a negative charge when suspended in water, they repel each other. This causes them to remain suspended rather than clumping together and settling out of the water. They might take days or even up to centuries to settle out!
Coagulation and flocculation are two separate processes, used in succession, to overcome the forces stabilising the suspended particles. While coagulation neutralises the charges on the particles, flocculation enables them to bind together, making them bigger, so that they can be more easily separated from the liquid.
Water coagulation diagram
The coagulation process in water treatment
This destroys the process whereby tiny particles repel each other and promotes their consolidation to bigger ones that are able to stick together. The bigger the particle, the easier it is to separate from the liquid. The use of coagulants for treating water goes all the way back to around 2000 BC when the Egyptians used almonds, smeared around vessels, to treat river water.
These larger ‘clumps’ of particles are called micro-flocs and still cannot always be seen by the naked eye. The water surrounding these newly formed particles should be clear – and this will signal that the particles’ charges have been neutralised. If it isn’t, more coagulant may be needed. Too much coagulant and the particles will revert to repelling each other – but predominantly by the reverse charge.
Rapid mixing ensures the coagulant is properly dispersed to promote particle collisions. The metal coagulant hydrolysis products formed within 0.01 to 1.0 seconds tend to be the most effective for destabilisation – this is why adjustment of pH and post-dosing of more coagulant is rarely effective after the initial coagulant addition.
One common type of rapid mixer is called a back-mix reactor, which normally consists of square tanks with vertical impellers. In many instances, they produce poor results, and WCS tends to design in-line mixers with velocity gradient control to provide the best conditions for rapid mixing.
Types of coagulants
Today, there are two types of coagulants that are most commonly used in water and wastewater treatment. Organic and inorganic.
Wastewater treatment cycle
Inorganic coagulants include:
Aluminium coagulants – e.g. aluminium sulphate, aluminium chloride and sodium aluminate
Iron coagulants – e.g. ferric sulphate, ferrous sulphate, ferric chloride and ferric chloride sulphate
Organic coagulants include:
Polyamines
Polydiallyldimethylammonium chloride (Poly DADMACs)
Polytannate
Inorganic coagulants
Both aluminium and iron coagulants have been proven to be very effective at removing most suspended solids. They offer a number of advantages:
Enable highly charged ions to give a high charge density to neutralise suspended particles, which allows hydrated inorganic hydroxides to form and produce short polymer chains that enhance microfloc formation and heavy floc
Capable of removing a portion of the organic precursors which may combine with chlorine to form disinfection by-products
Low unit cost and widespread availability
They have some disadvantages:
They create large volumes of floc, rich in metal, which must be disposed of in an environmentally appropriate manner, which can add significant cost to disposal
They can significantly alter the pH of the water, where pH is critical for effective coagulation, necessitating pH control. They also require corrosion-resistant storage and feed equipment.
Aluminium sulphate and chloride, ferric sulphate and chloride and ferrous sulphate are highly acidic, destroy alkalinity and lower pH. Sodium aluminate, on the other hand, will add alkalinity and raise pH.
Organic coagulants
Both polyamine and poly-DADMAC coagulants have been proven to be very effective at removing most suspended solids. Tannates are particularly good at oils and fats. They offer a number of advantages:
Enable relatively low charge density to neutralise lower charged suspended particles, more effectively. Produce longer polymer chains that enhance microfloc formation without metals or hydroxides
Capable of removing a portion of the organic precursors which may combine with chlorine to form disinfection by-products
Produce small floc volume
Liquid forms, non-corrosive, ready for direct use.
Do not impact and are rarely or marginally affected by pH
They have some disadvantages:
Higher unit cost
High dosages are needed if charge demand is high
Low-density floc – does not always settle well.
The most commonly used inorganic chemical coagulants in water treatment
Aluminium sulfate is the most commonly used chemical for coagulation in wastewater treatment. Additional commonly used coagulants include sodium aluminate, ferric sulfate, and ferric chloride.
Aluminium Sulfate
Aluminium sulphate is the most widely used aluminium coagulant. It is available in a number of solid forms such as block, kibbled, or ground and is also available as a solution. When added to water, the acidic coagulant and the natural alkalinity of the water reacts to form an aluminium hydroxide floc, which usually consists of calcium bicarbonate. pH control is important in coagulation, for both the removal of turbidity and colour and also to maintain satisfactory minimum levels of dissolved residual aluminium in the clarified water.
Sodium Aluminate
Sodium aluminate is formed by combining sodium oxide and aluminium oxide. Solid forms of this chemical usually contain 70-80% sodium aluminate, while liquid forms contain around 30% sodium aluminate. Due to the low molecular weight of AI, sodium aluminate solutions reduce chemical sludge production compared to iron. Moreover, aluminates raise the alkalinity of the water, eliminating the need for lime or hydroxides.
Ferric Sulfate
Ferric sulfate is a type of iron coagulant that is often used in conjunction with chlorine and can provide a denser floc than aluminium sulfate. Compared to alum, ferric sulfate has some advantages; for example, the flock particles of ferric hydroxides have a higher density than alum flocks and are more easily removed by sedimentation. However, there are also disadvantages as it produces a significantly heavier hydroxide sludge and it is difficult to dissolve.
Ferric Chloride
Ferric Chloride works as a flocculant and coagulant. It is versatile in the water treatment industry and is an alternative to ferric sulfate. It generally promotes faster sedimentation, especially in cold water. However, it is the less popular choice, as chloride can increase water’s corrosivity.
Which coagulant should you choose for water treatment?
In water treatment, metal coagulants such as the ones listed above are commonly used. Availability and affordability are the key considerations that generally influence the coagulant used. Aluminium sulfate is commonly available and affordable as well as being very effective.
However, other types of coagulants are also available:
Synthetic coagulants may have high charge densities on relatively large molecules. Depending on how they are made, some of the synthetic derivatives may behave as a flocculant.
Biopolymer coagulants from natural sources (such as fungi and plant sources). Generally, these produce less sludge, are less toxic, and are considered to be safer.
What is flocculation in wastewater treatment?
Following coagulation (“Charge Neutralisation”), a second process called flocculation needs to take place. This is the growth of small, neutral particles into larger particles. Flocculants are the agents which promote this clumping of fine particles into ‘floc’ that can then be readily separated from the water. They are invariably polymers.
The flocculation process is a gentle mixing stage that increases the size of the particles from micro-floc to large, visible suspended particles called pin-flocs. Additional collisions between pin-flocs cause them to produce even larger, ‘macro-flocs’. The flocculants aid in this by being long-chain polymers with low charge to involve entanglement, enhanced van der Waal’s forces, and hydrogen bonding between the particles. Once these flocs have reached an optimum size and strength, the water is ready for solids-liquid separation. This can be filtration, centrifugation, sedimentation, or flotation.
The role of polymers in flocculation
Polymers are a range of water-soluble macromolecular compounds that have the ability to stabilise or enhance flocculation of the constituents in a body of water. They are added as part of the flocculation process to help strengthen and increase the settling weight of the floc.
Polymers can be either natural or synthetic. Natural polymers also date back to ancient times, with Sanskrit literature from around 2000 BC referencing the use of crushed nuts to clarify water. Natural polymers are virtually free of toxins and are biodegradable. Synthetic polymers are more commonly used because they are more effective, reliable, reproducible, and cost-effective.
Water purification cycle at a plant
What does the coagulation and flocculation process remove in wastewater treatment?
Coagulation and flocculation remove a large number of organic compounds as well as suspended particles, including inorganic precipitates. The process removes particles and dissolved matter; however, the water may still contain pathogens, including viruses and bacteria. Pathogens are generally only removed if they are attached to the dissolved substances that are removed by coagulation and flocculation.
This is the first step in wastewater treatment and turning it into potable water—coagulation and flocculation remove many of the particles that make it complicated to disinfect water. Thanks to coagulation and flocculation, a smaller amount of chlorine needs to be added to disinfect the water. And using less chlorine saves money and makes the water safer.
Conclusion
Coagulation and flocculation are two, separate, crucial parts of water and wastewater treatment. Coagulation destabilises the minute suspended particles by static charge neutralisation, while flocculation helps them to bind together to form much bigger morphologies, so they can be more easily separated from the liquid phase.