How to choose multi-rake bar screen?
Bar screens are automated mechanical systems that remove large solids, such as cans and driftwood, from water streams.
Bar screens generally operate in a conveyor-like system. Solids are picked up by a bar or wire filter that allows the water through. The filter is either intermittently or continuously moved through and out of the water channel to a motorized cleaning and trash area. This prevents the system from failing due to clogging and keeps water flow steady.
Older bar screens required manual cleaning. However, the process is generally too labor-intensive to be practical, making them obsolete when compared to the more cost-effective mechanical systems.
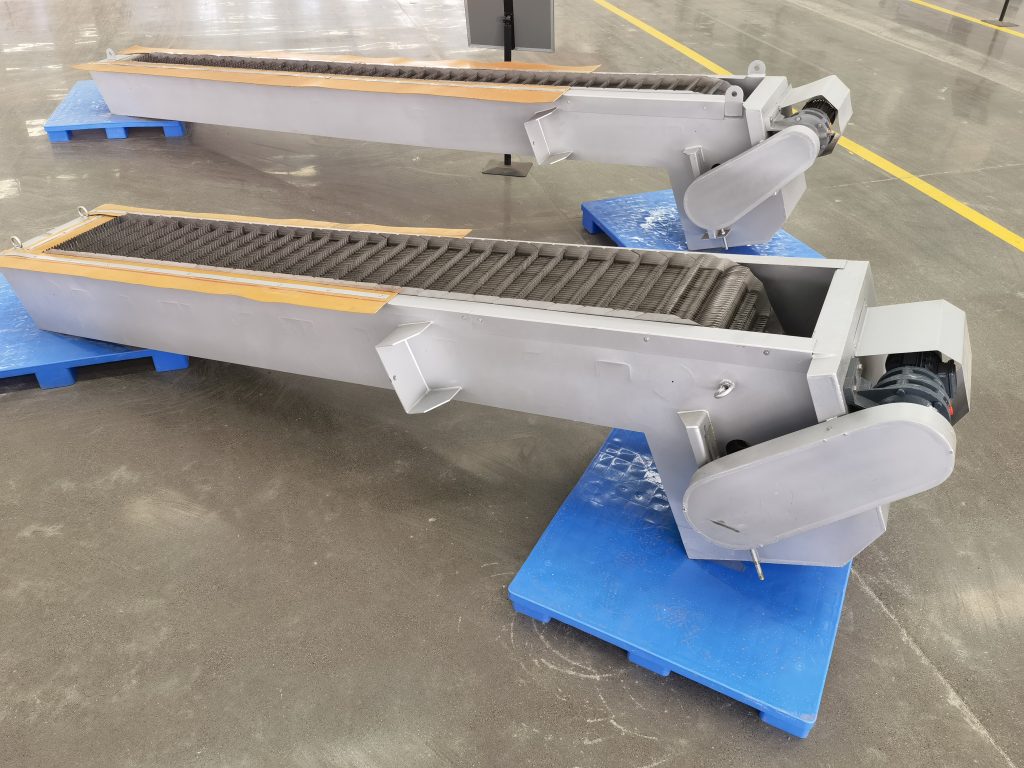
Selection Criteria
In order for a bar screen to operate effectively, the capacity of the filter and cycle rate must be designed to output the desired water flow rate. Conditions that influence this are the size and concentration of debris, the input flow rate of the current, and the cross-sectional area of the channel. Design specifications of the bar screen that affect the outcome include mesh size or wire diameter and the speed of the recycle system.
Mesh (sieve) size or wire diameter determines the size of the holes or open space in the filter, thus determining what particles can be captured. Mesh sizes vary by series, but larger diameter wires and fewer squares per inch result in a finer filter. Finer filters will capture smaller-size material but will consequently become saturated and clogged faster than screens with larger openings.
Cycle rate is how quickly a bar screen moves. A screen that cycles faster can handle larger volumes of incoming solids without becoming clogged. Screen cycle rate is limited by how well it can pick up and clean off solids during the removal stage. Screens that remove too fast may not effectively pick up and filter the material or may not allow sufficient time for solids to be removed.
Applications
Another important factor to consider is whether an inline strainer would perform better than a bar screen. Inline strainers allow material screens to be moved to a scraper for cleaning via a simple hand wheel or actuation motor. They are ideal for processes where process flow must remain uninterrupted during filtration.
Bar screens are better suited for higher solids concentrations, and many times will slow down the flow rate of the stream. In streams with a complex concentration of solids, multiple bar screens (of gradually finer size) are placed in sequence followed by pumps to reestablish flow rate. Inline strainer(s) come later to maintain flow and catch the remaining solids.
Inline strainers tend to have lower capital and maintenance costs than bar screens. Because of their closed system design, strainers also boast safer conditions for personnel when hazardous materials are involved.
The most common uses for bar screens are in the water and wastewater treatment industry. This includes treating water sent to cooling towers for nuclear power plants, wastewater from industrial sources, and water prepared for commercial use.